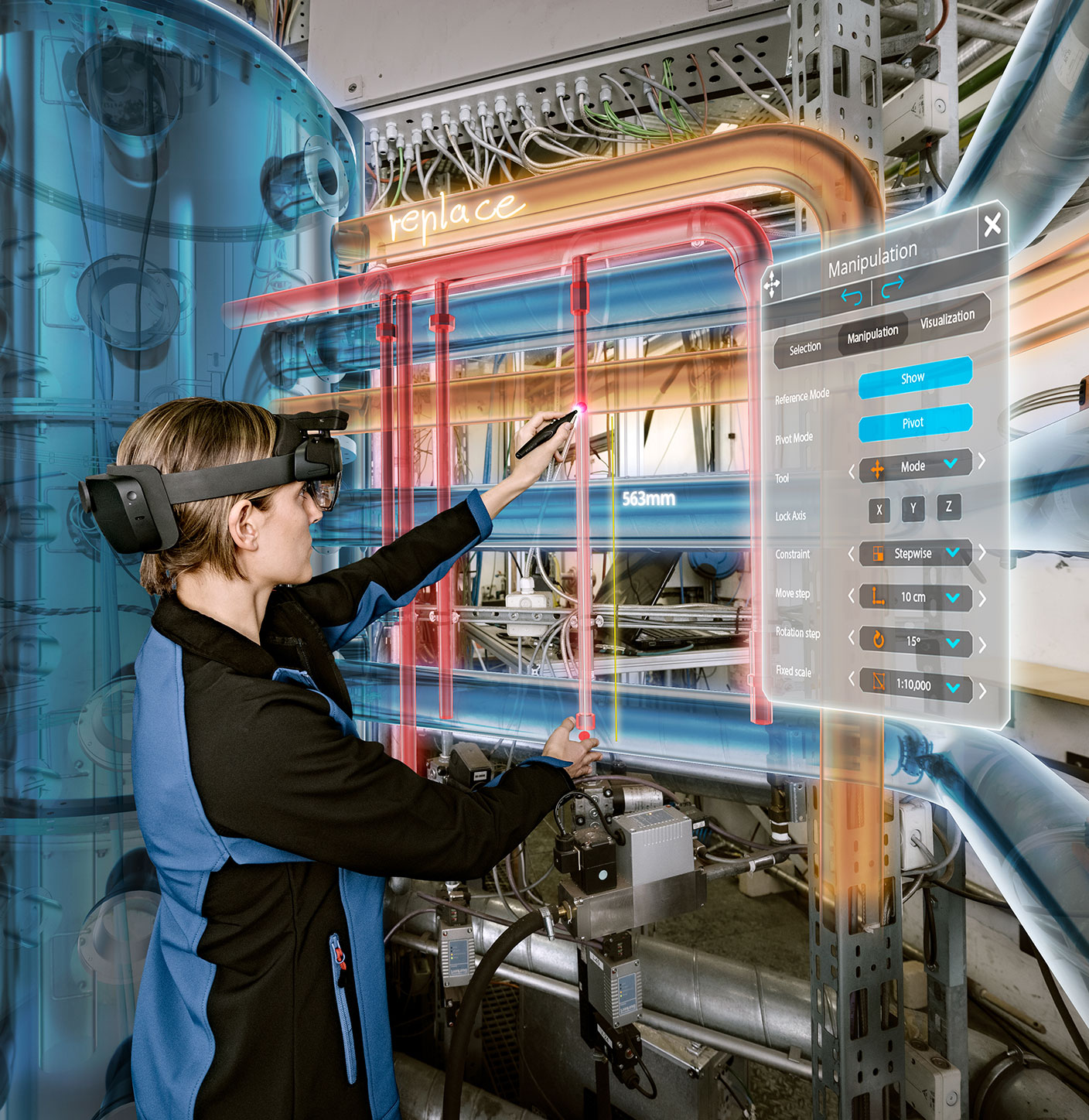
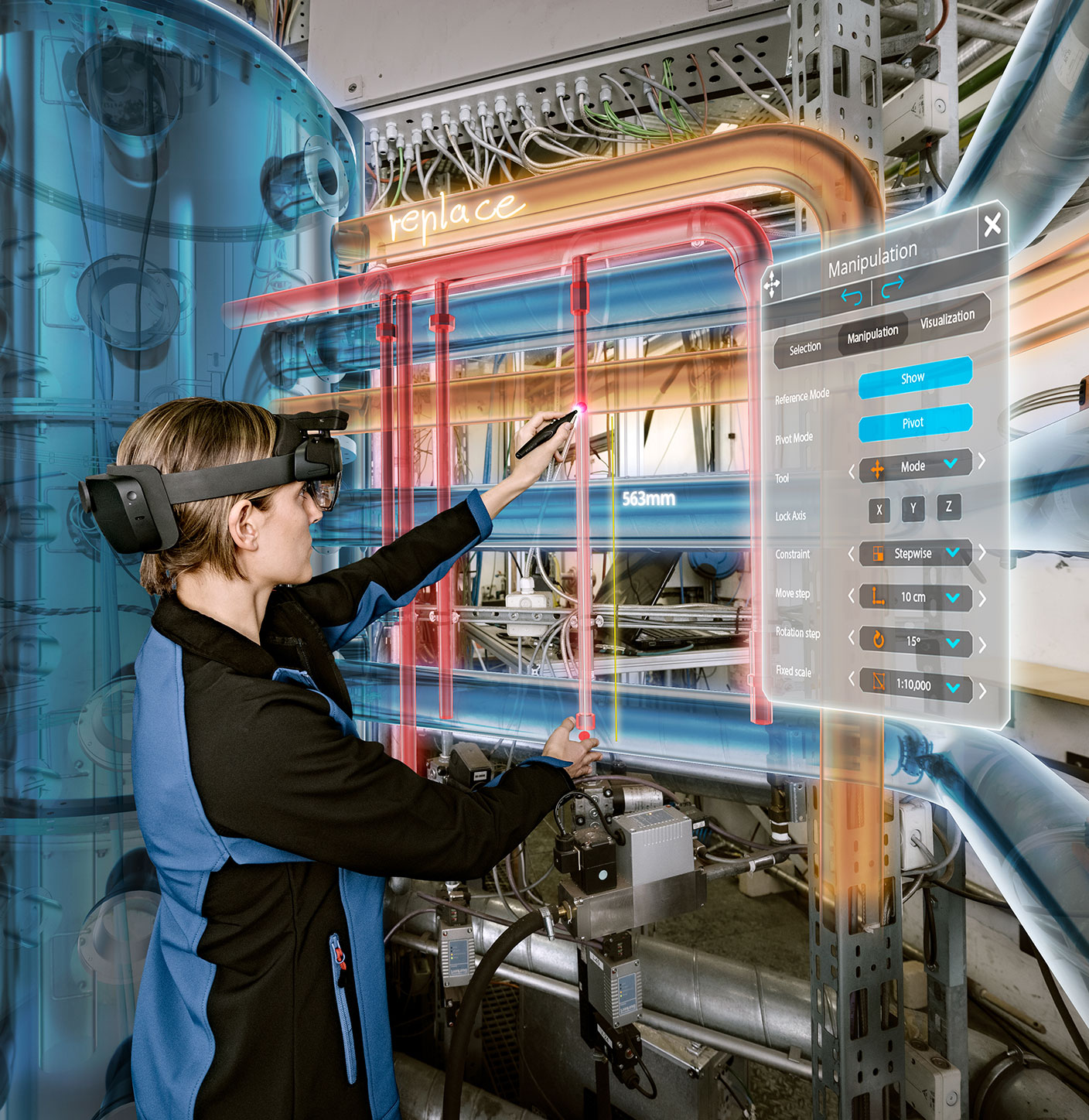
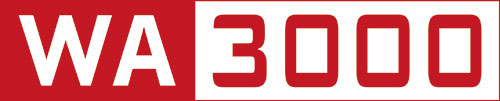
Innovative technology
CAD models as holograms. Modifiable and collaboratively
editable. Augmented Reality (AR) is expected to revolutionize workflows in factory planning. At BASF, the
world’s largest chemical company, the use of AR already shows great potential.
The planning of a complete plant or even individual production lines has a significant influence on investment
and operating costs. In addition, capacity utilization and the product quality itself are strongly dependent on
good planning. However, virtual planning and reality still too often do not match. Data in the system becomes
obsolete. Design faults make complex construction projects more difficult. Incorrect planning causes costs to
skyrocket.
Currently, working in the field is the focus of attention. So how can production environments be optimally planned? How can companies integrate new plants, machines, and pipelines without stopping ongoing operations? And what will future workflows of engineers look like? The AR expert Holo-Light aims to take working with CAD models to a new level of collaboration and efficiency using augmented reality software.
With its Augmented Reality Engineering Space (AR3S), the company wants to close the gap between virtual planning and what is ultimately real. Teams of engineers at BASF have already integrated the new type of AR engineering into their daily work practice: Using AR3S, they efficiently compare digital planning data with the real factory environment and document changes in real time on site.
This means that engineers print out paper plans, draw in additional data from the CAD model and then – equipped with clipboards – check the designs in the field. This is a time-consuming and above all an error-prone process. For example, pipelines are incorrectly planned or not considered, power lines are not planned, or ventilation ducts are only considered with rough positioning.
The same applies to factory structures, already existing cable harnesses, machines, and cells. Space requirements, connections or possible collisions are clear challenges in investment decisions.
It can easily happen that a factory plant has to be subsequently adapted at great cost or even shut down temporarily.
Even at BASF, planning complex plants and pipelines without a real reference on a 2D screen often proved to be tricky. The chemical company needed a tool to visualize and edit components in the factories – i. e. on site – true to scale in the existing environment. It should also be possible to feed back the data for further planning. BASF now sees augmented reality as a key technology for the complete digitalization of factory planning and is actively promoting the use of AR in practice.
With the help of AR3S, engineers can retrieve planned pipelines and assemblies directly to their intended destination.
Using the digital twin, it is thus possible to quickly determine whether planning and reality are compatible or whether changes are still required in the project.
"What-if" test scenarios also give engineers a better understanding of their planned factory layout. And even during the engineering phase, on-site monitoring helps to detect and eliminate deviations early on before they lead to subsequent problems.
Currently, working in the field is the focus of attention. So how can production environments be optimally planned? How can companies integrate new plants, machines, and pipelines without stopping ongoing operations? And what will future workflows of engineers look like? The AR expert Holo-Light aims to take working with CAD models to a new level of collaboration and efficiency using augmented reality software.
With its Augmented Reality Engineering Space (AR3S), the company wants to close the gap between virtual planning and what is ultimately real. Teams of engineers at BASF have already integrated the new type of AR engineering into their daily work practice: Using AR3S, they efficiently compare digital planning data with the real factory environment and document changes in real time on site.
From Paper to Augmented Reality
For more than 30 years now, engineers have been using 3D renderings of CAD models to check their manufacturability. Within the framework of classic workflows, they work in CAD systems such as AutoCAD: on 2D screens and on a reduced scale. The comparison with reality is then usually done manually.This means that engineers print out paper plans, draw in additional data from the CAD model and then – equipped with clipboards – check the designs in the field. This is a time-consuming and above all an error-prone process. For example, pipelines are incorrectly planned or not considered, power lines are not planned, or ventilation ducts are only considered with rough positioning.
The same applies to factory structures, already existing cable harnesses, machines, and cells. Space requirements, connections or possible collisions are clear challenges in investment decisions.
It can easily happen that a factory plant has to be subsequently adapted at great cost or even shut down temporarily.
Even at BASF, planning complex plants and pipelines without a real reference on a 2D screen often proved to be tricky. The chemical company needed a tool to visualize and edit components in the factories – i. e. on site – true to scale in the existing environment. It should also be possible to feed back the data for further planning. BASF now sees augmented reality as a key technology for the complete digitalization of factory planning and is actively promoting the use of AR in practice.
AR workplace for engineers
To be specific, BASF engineers use the Augmented Reality Engineering Space AR3S for the planning and expansion of intermediate product plants. In combination with Microsoft's AR glasses HoloLens, the software suite offers experts a tool for visualizing, manipulating and collaboratively processing CAD data (e. g. from PLM systems) as holograms in a real environment.With the help of AR3S, engineers can retrieve planned pipelines and assemblies directly to their intended destination.
Using the digital twin, it is thus possible to quickly determine whether planning and reality are compatible or whether changes are still required in the project.
"What-if" test scenarios also give engineers a better understanding of their planned factory layout. And even during the engineering phase, on-site monitoring helps to detect and eliminate deviations early on before they lead to subsequent problems.