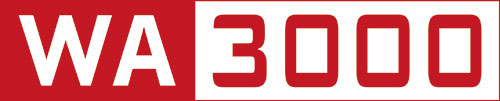
Robotics
For this
purpose, magnetic points are embedded in the floor of the production area at a certain distance. Sensors on the
automated guided vehicles use this orientation aid to determine their exact position and report it to the
central guidance system. The central guidance system takes over the traffic simulation and vehicle control and
ensures that all AGVs are coordinated to deliver the components to the right place at the right time along the
most optimal route, on 11 intersecting loops.
Intuitive and
The master control of the automated guided vehicle system is directly connected to the Mercedes-Benz production
control system. In this way the AGVs automatically adapt to the higher-level production planning without the
need to intervene in the guidance system of the AGV.
In the event of a break in production – for example on public holidays or long weekends – the AGVs automatically go into stand-by mode, which can last up to 92 hours. If production restarts within this period, the vehicles automatically resume their activities. The AGV guidance system also ensures fully automated charging management.
The AGVs drive autonomously to the charging stations and are thus ready for operation 24/7. A graphical user interface (GUI) allows new routes to be planned and simulated easily and intuitively. The system linkage, which takes place at the same level as the production system, allows very quick and easy adaptation to changes in the production infrastructure, for example to integrate new model series. Another advantage of free, inductive magnetic grid navigation: In the harsh environment of the body shop, optical sensors can be contaminated by welding dust, for example. Navigation using magnetic grids is insensitive and robust, which makes it particularly reliable.Milestone in intelligent
"The intelligently networked automated guided vehicle system ensures smooth plant linkage and more safety for
the workers in the body-in-white production," summarizes Michael Jürgens. The automated guided vehicle system in
the body-in-white of the production plant in Tuscaloosa is a forward-looking pilot project. "We are proud of the
successful implementation of the project; it is considered by all those involved to be a milestone in
intelligent intralogistics. And we are even more pleased about the continued cooperation and the trust in our
know-how," concluded Felix Tschorn.
▪
Author: Sandra Neumeier,
Marketing Manager at KUKA
Intuitive and
central guidance concept
The master control of the automated guided vehicle system is directly connected to the Mercedes-Benz production
control system. In this way the AGVs automatically adapt to the higher-level production planning without the
need to intervene in the guidance system of the AGV.In the event of a break in production – for example on public holidays or long weekends – the AGVs automatically go into stand-by mode, which can last up to 92 hours. If production restarts within this period, the vehicles automatically resume their activities. The AGV guidance system also ensures fully automated charging management.
The AGVs drive autonomously to the charging stations and are thus ready for operation 24/7. A graphical user interface (GUI) allows new routes to be planned and simulated easily and intuitively. The system linkage, which takes place at the same level as the production system, allows very quick and easy adaptation to changes in the production infrastructure, for example to integrate new model series. Another advantage of free, inductive magnetic grid navigation: In the harsh environment of the body shop, optical sensors can be contaminated by welding dust, for example. Navigation using magnetic grids is insensitive and robust, which makes it particularly reliable.
Milestone in intelligent
intralogistics
"The intelligently networked automated guided vehicle system ensures smooth plant linkage and more safety for
the workers in the body-in-white production," summarizes Michael Jürgens. The automated guided vehicle system in
the body-in-white of the production plant in Tuscaloosa is a forward-looking pilot project. "We are proud of the
successful implementation of the project; it is considered by all those involved to be a milestone in
intelligent intralogistics. And we are even more pleased about the continued cooperation and the trust in our
know-how," concluded Felix Tschorn.
▪Author: Sandra Neumeier,
Marketing Manager at KUKA
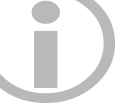