Laser beam welding in vacuum without pores and welding spatters
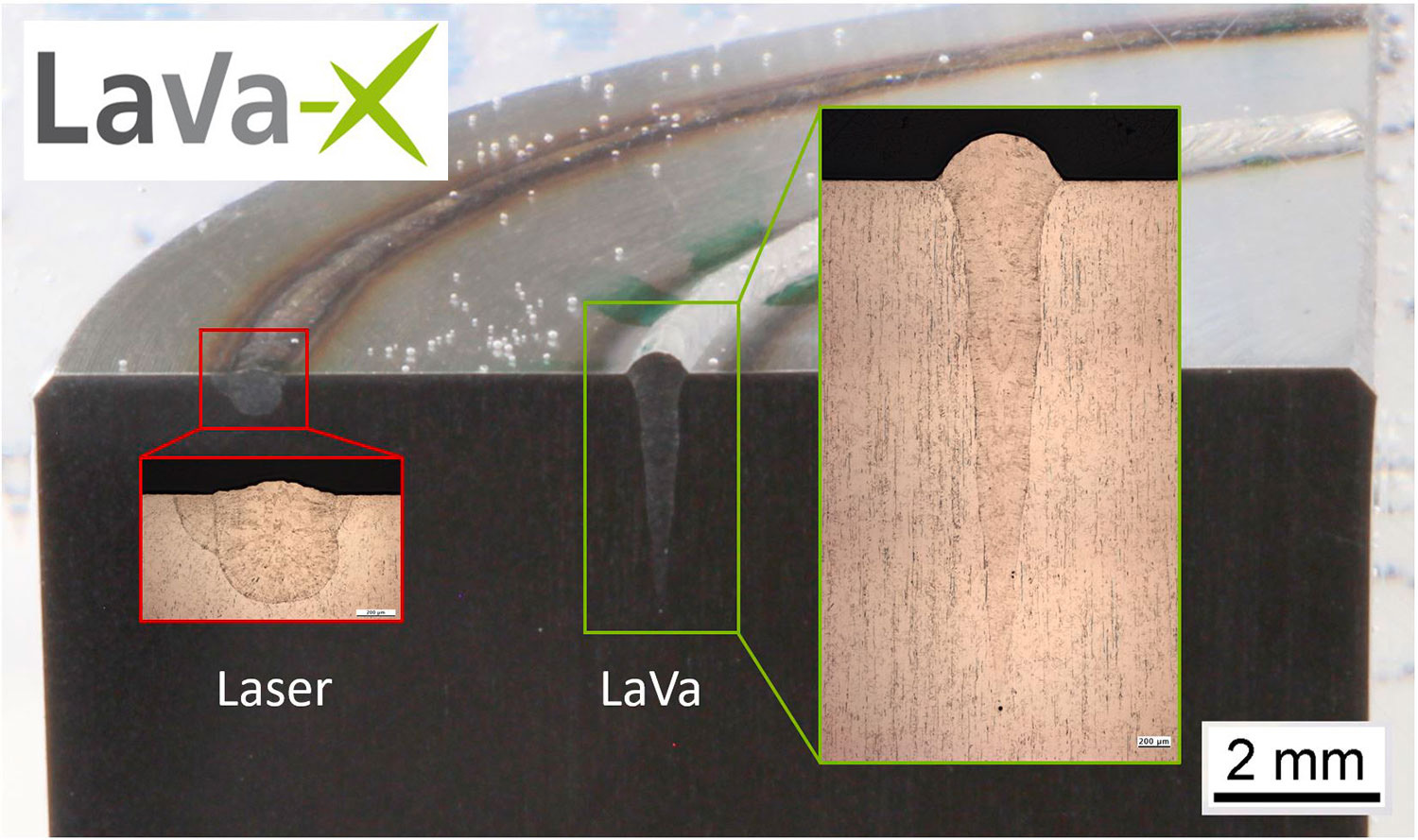
Comparison of a weld seam at 500 W between laser welding and LaVa
LaVa-X from Aachen has developed a machine that uses the LaVa process to increase the quality and
welding depth of laser welding of metals.
The process increases the quality and productivity of laser welding while reducing investment and operating
costs.
Due to the significant increase in efficiency, welding seams with a depth of approximately one millimeter can be produced with a beam power of just 200 watts. In addition, the reduced heat input leads to less heating of the components and avoids distortion. This is particularly useful with temperature-sensitive materials such as titanium or housings in which the electronics are already installed.
Due to the significant increase in efficiency, welding seams with a depth of approximately one millimeter can be produced with a beam power of just 200 watts. In addition, the reduced heat input leads to less heating of the components and avoids distortion. This is particularly useful with temperature-sensitive materials such as titanium or housings in which the electronics are already installed.
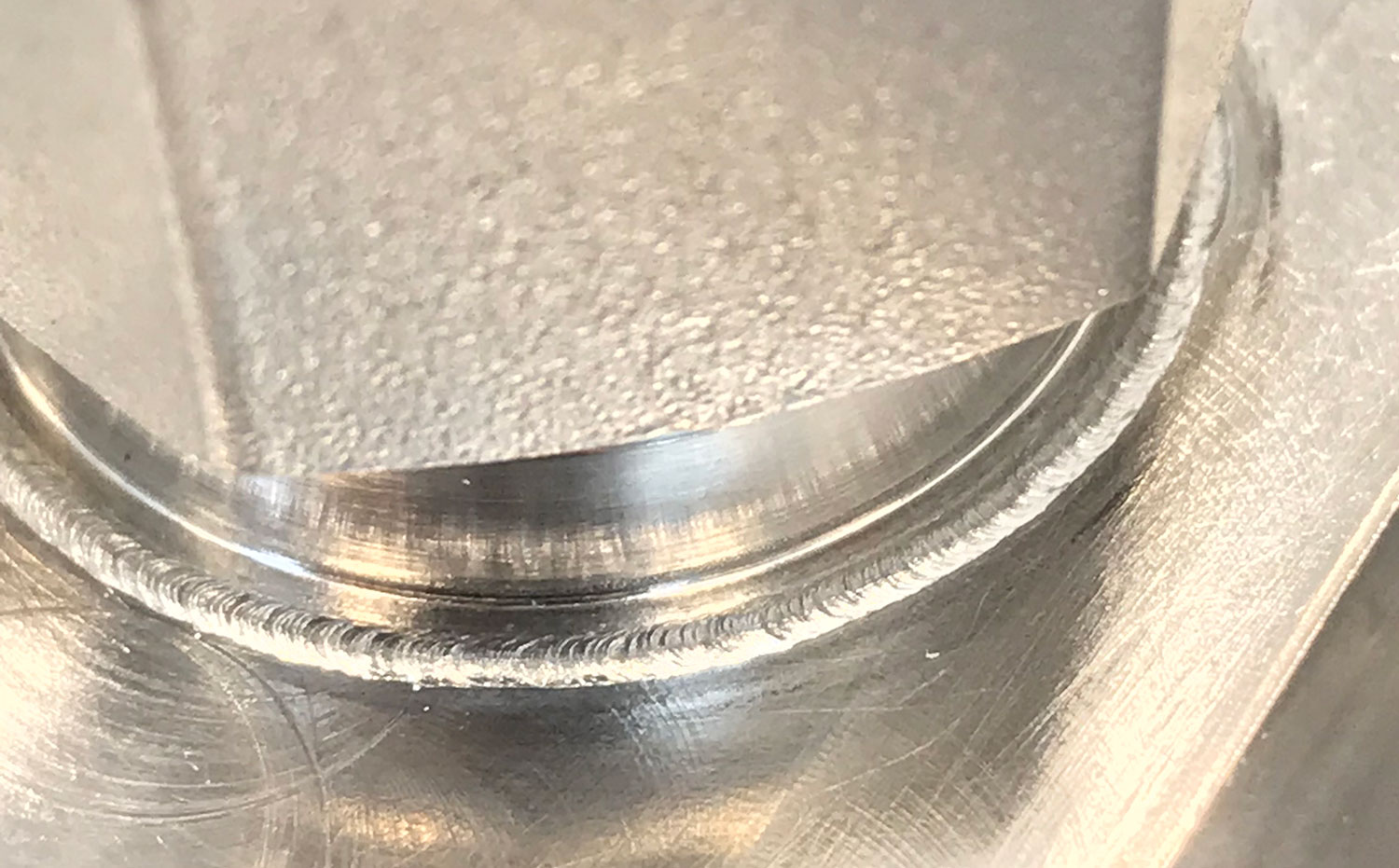
LaVa weld seam on a sensor housing