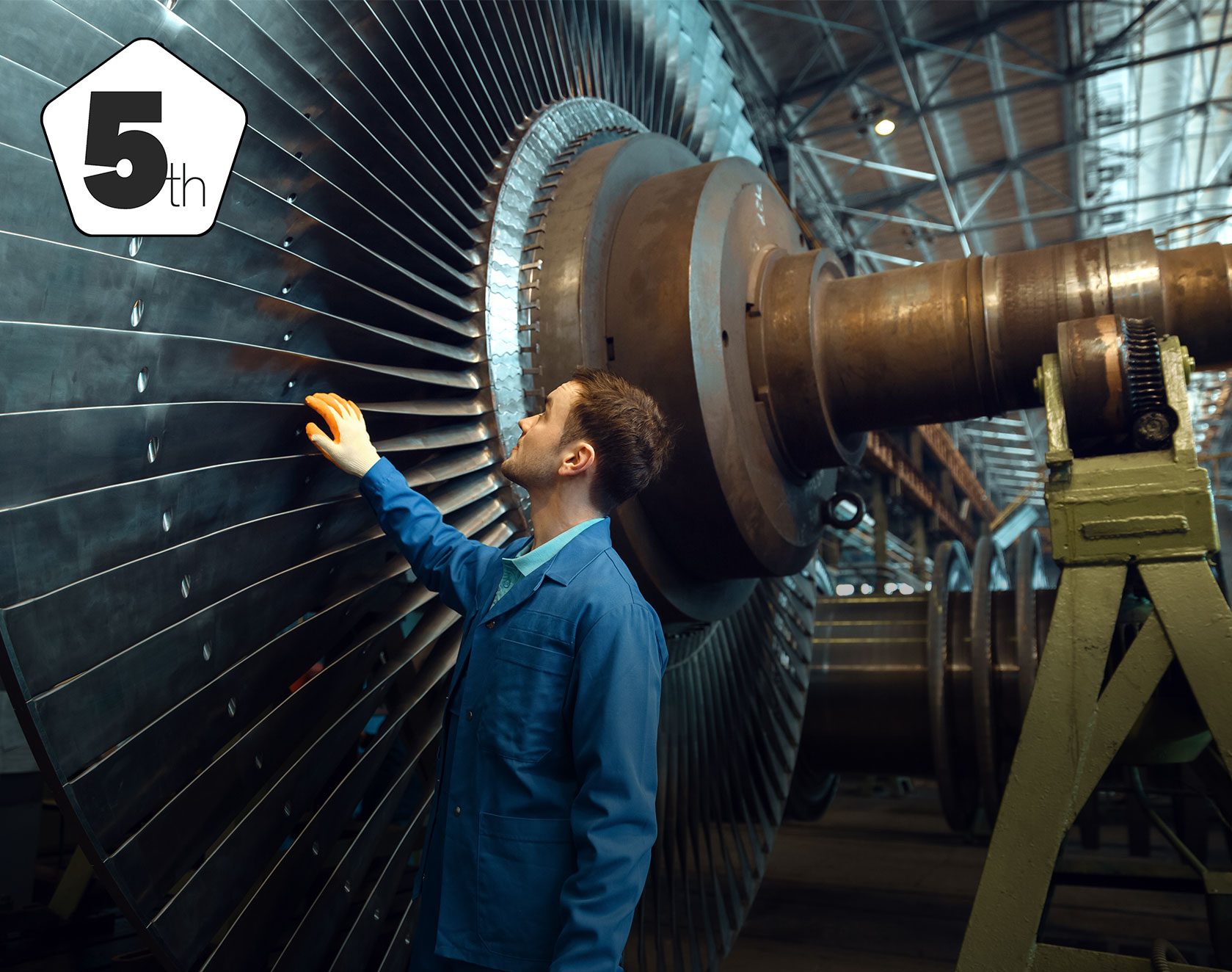
Reducing error costs –
full transparency through intuitive software
5i.Quality app enables holistic tracking of quality issues
5thIndustry supports preventive quality work with the cloud-based app 5i.Quality – so companies can easily
and effectively eliminate causes of defects and track measures, without email chains and paperwork.
Automotive suppliers, medical technology manufacturers and high-tech machine builders in particular can
leverage productivity potential in this way.
5thIndustry supports preventive quality work with the cloud-based app 5i.Quality – so companies can easily
and effectively eliminate causes of defects and track measures, without email chains and paperwork.
Automotive suppliers, medical technology manufacturers and high-tech machine builders in particular can
leverage productivity potential in this way.