.jpg)
.jpg)
Automated production
Automated production
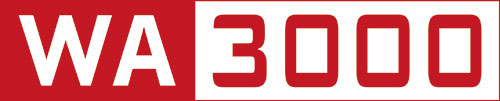
The managers at the medium-sized company Hugo Benzing GmbH & Co. KG in Korntal-Münchingen quickly recognized this new trend towards sustainable electric vehicles.
Protection against battery overheating
The world's leading manufacturer of safety elements also realized its expertise to be useful for the construction of electric cars.This is how the safety experts started developing bursting membranes and bursting disks for e-mobility.
The patented safety valves release pressure into the ambient air in the event of thermal overheating in the battery.
By preventing an increase in pressure in the battery, they ensure the safety of the electric car.
High safety requirements in the production process
High safety requirements and constant quality controls in the production process are necessary to
manufacture this vent valve. The valve consists of three parts, which are assembled in an automated
production cell at Benzing.
"We initially built the parts by hand," retrospects Managing Director
Christian Benzing. But it soon turned out that the demand for these bleeder valves from the automotive
industry would increase dramatically. "We therefore needed large quantities," says Benzing. The
enormous
growth in capacity could only be achieved through automation. In addition, the safety tests of the
individual parts could now be standardized according to defined, programmed processes and with the help
of modern technology. This is where the expert knowledge of the mechanical engineering and automation
company, WAFIOS Tube Automation GmbH from Simonswald in the Black Forest, has come into play.